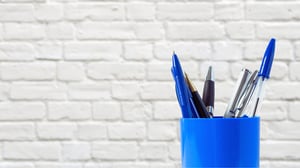
BIC Factory Planning Reimagined
INDUSTRY
Consumer ProductsSOLUTION
Connected Planning & FulfillmentOFFERING
Production & Factory PlanningTECHNOLOGY
Blue YonderHow BIC cut changeovers & unlocked millions in hidden capacity
BIC is a global consumer products icon—producing more than 32 million pens, lighters, and razors every day. But behind the brand is a highly complex packaging and manufacturing operation where precision matters, especially at high volume. At the company’s flagship Charlotte, NC facility, planners were still relying on manual Excel-based scheduling tools that could only look out three days. This limited visibility created a chain reaction of inefficiencies.
With a narrow planning horizon, the team couldn’t preempt bottlenecks or optimize line sequencing. Machine changeovers were frequent and uncoordinated. Tooling and labor assignments were often mismatched. And with demand climbing, the company faced a stark decision: Either find more throughput internally or fund an expensive new facility. The stakes weren’t just high—they were imminent.
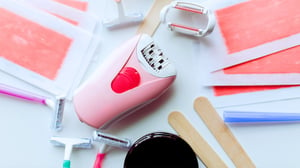
From reactive schedules to strategic sequencing
- 01 Audit what’s broken
- 02 Architect the future state
- 03 Codify tribal knowledge
- 04 Optimize for execution
- 05 Enable adoption and scale
Uncovering the root cause of inefficiency
Designing a smarter, more sustainable planning model
We co-designed a two-week factory planning model tailored to BIC’s operations—grounded in Blue Yonder’s Factory Planning solution. The new engine accounted for product line rules, labor constraints, order need dates, and changeover reduction logic—all configurable, all visible.
Capturing experience and translating it into automation
Putting powerful insights into planners’ hands
The automated scheduling tool delivered clear, constraint-aware production sequences—minimizing unplanned changeovers and improving throughput. Planners gained a real-time view of capacity and tooling, while supply chain and operations teams aligned around a single, trustworthy plan.
Driving alignment beyond go-live
Proof that planning can be a profit center
-
40% reduction in changeovers: By eliminating one to two unnecessary changeovers each week, the team dramatically improved line efficiency and product flow.
-
Increased weekly capacity by 20+ hours: Enough to defer capital expenditure on a new packaging facility—saving millions in projected costs.
-
1,600% faster scheduling: What once took hours was now executed in minutes, freeing planners to focus on value-added tasks.
-
Improved collaboration: A single, trusted production plan now connected floor supervisors, planners, and supply chain managers—driving greater customer service levels and internal alignment.
Let's build what's next.
Scale your operations by unlocking hidden potential—not by spending more, but by planning smarter. If your factory floor is running on tribal knowledge and time-consuming spreadsheets, it’s time to rethink what’s possible.