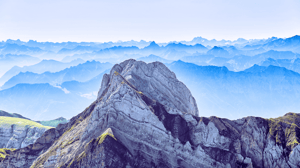
Five Lenses Framework
Technology alone won’t transform your supply chain. A holistic, execution-ready strategy will.
Supply chain excellence, delivered
Our core values set the tone for everything we do at Spinnaker SCA. By starting with the “why,” our team guides you to best “what” and “how” for your business and desired outcomes. And this all comes together using our Five Lenses Framework.
The Five Lenses Framework is our proven supply chain consulting methodology. It is a holistic approach that examines the five key areas of digital business transformation: People, Process, Technology, Policies, and Metrics. This structured approach ensures we build a complete and agile solution to help you achieve supply chain excellence.
A holistic approach to digital supply chain transformations
Do we have the right team and capabilities in place? Are any changes to roles and responsibilities across the organization understood and agreed? Are users properly trained to perform their roles and drive continuous improvement efforts?